Никогда не слишком рано выбирать свои пластмассы. Аль Тимм
При разработке оптимального продукта или дизайна детали, который соответствует целям, поставленным отделом разработки продукта, материал, который вы выбираете, может иметь большое значение. Материалы могут сделать или нарушить вашу способность выполнять дизайнерские спецификации и функциональность продукта. Поиск подходящего материала может даже превысить вашу первоначальную концепцию, особенно если вы рассматриваете смолы.
С железного века металл стал материалом выбора благодаря его ковкости и прочности. Однако сегодня дизайнеры применяют пластмассы в растущем наборе деталей и компонентов продукта. Полимеры имеют несколько преимуществ перед металлом. Например, полимеры могут уменьшить вес и время обработки.
Металлопластиковые конверсии для сложных литьевых деталей становятся все более распространенными в разработке продукта. Это краткое сравнение показывает, почему.
Металлические детали:
- Требует дорогостоящей высокоточной обработки
- Должна быть индивидуально обработана
- Необходима вторичная отделка для предотвращения коррозии
- Проводить тепло в высокотемпературных условиях
Пластиковые детали:
- Требуется только одна форма
- Может производиться быстро и легко в больших объемах
- Естественно коррозионно-стойкие, устраняет большинство вторичных отделочных операций
- Служит в качестве изоляторов в высокотемпературных условиях из-за низкой теплопроводности
Возникновение пластика осуществляется, поскольку полимерная наука делает огромные успехи в исследованиях и разработках, что приводит к безудержному росту выбора материалов. В то же время быстрое продвижение в способности связывать различные смолы с наполнителями и добавками может обеспечить огромное количество структурной целостности.
При правильном выборе материала, в сочетании с оптимизацией дизайна, пластмассовые компоненты могут быть такими же прочными, как металл, весят меньше и потенциально обеспечивают огромную универсальность. Существует почти бесконечное количество комбинаций смолы и наполнителей в машиностроении. При определении того, какой из этих материалов лучше всего подходит для вашего проекта, время, затраченное на привлечение опытного литьевого формования, стоит того.
Идея удовлетворения потребностей в смоле в начале процесса проектирования с партнером по литьевому формованию является идеальной. Глубинные знания компании Molder помогут вам в наиболее эффективных и экономичных процессах для ваших промышленных применений. Их экспертные знания о характеристиках производительности также могут предоставить вам возможность максимизировать преимущества продукта для пользователя.
Вот основные соображения для оценки вашего проекта с точки зрения материалов, включая спецификации, компоненты смолы и коэффициенты эффективности формования.
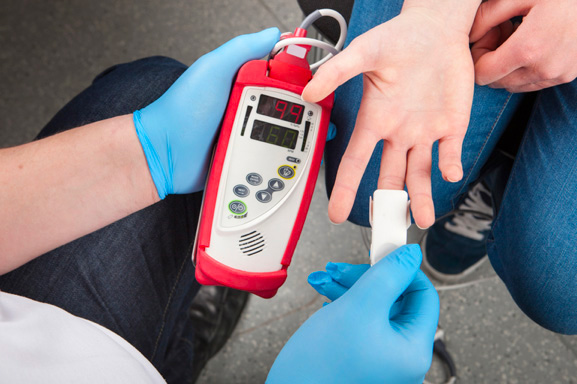
Сосредоточение внимания на среде использования продукта
Когда дело доходит до выбора смолы или смоляного компаунда, который будет использоваться при формовании вашего проекта, зная, как будет использоваться конечный продукт, где он будет использоваться, и требования, которые он будет помещать, приближают вас к созданию лучший выбор. Рассматриваемые факторы включают:
- Прочность
- Жесткость
- Химическая устойчивость
- Термостойкость
- Гибкость
- Ударопрочность
- Внешность
- Проводимость / экранирование
- Фрикционные свойства
- Сопротивление пламени
Приоритетность этих характеристик дает вам возможность сортировать доступные смолы, которые улучшат ваш конечный продукт.
Путем взвешивания этих параметров в прямом отношении к вашему приложению вы устраните много догадок и возможного отступления, когда речь идет о выборе правильной смолы. Вот еще несколько подробных соображений, которые позволят определить правильный материал:
- Физическая нагрузка. Каковы ожидания в отношении воздействия и весовых требований для обеспечения того, чтобы материал соответствовал условиям повседневной усталости, а также отвечал любым требованиям безопасности?
- Механическая функция детали. Может ли продукт / деталь выдерживать крутящий момент и требуемые циклы?
- Тепловые условия. Будет ли продукт / деталь противостоять колебаниям и экстремальным температурам?
- Химическое воздействие. Будет ли продукт / деталь подвергаться промышленной среде и / или операциям, которые могут вносить суровые вещества, которые могут разрушать или искажать пластмассовые компоненты, такие как смазки, масла или растворители?
- Использование разнородных материалов. Препарат может потребовать многоразовой технологии или сверхмодулирования (процесс, посредством которого одна часть создается с использованием двух или более различных материалов в комбинации), чтобы обеспечить эффективное взаимодействие смолы и совместимость с другими компонентами системы.
- Применение высокотемпературной смолы. Материалы в этой категории труднее работают, благодаря более высоким температурам плавления. Эти качества требуют тщательной оценки всех аспектов применения, от безопасности до процессов формования.
Выбор смолы
Оценка ваших потребностей в проекте сужает широту материалов, подходящих для продукта или его части. Характеристики смолы будут определять правильный материал в соответствии с требованиями части.
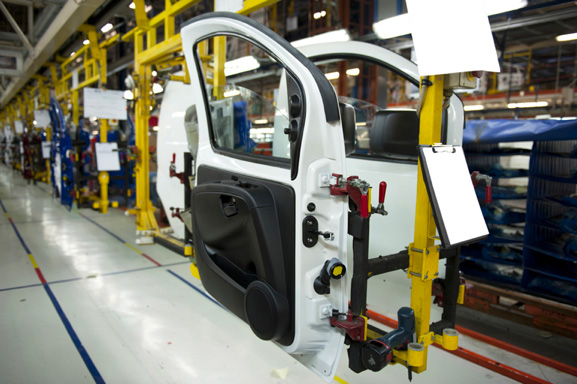
Долговечность
Производители, которые производят надежное электронное оборудование, имеют клиентов, которые рассчитывают на то, что их устройства будут работать в сложных жизненных условиях и выдерживать удар, удар и вибрацию. Поэтому ударопрочность приводит к выбору поликарбоната (ПК), акрилонитрилбутадиенстирола (АБС), полиэтилентерефталата (ПЭТ) и нейлона для формования прочных корпусов.
Чтобы повысить способность продукта выдерживать толчки и капли, литьевые формовочные машины могут добавлять эластомерные полимеры в расплав. Поскольку эти добавки являются эластичными по своей природе, они деформируются при ударе без сбоев, а их материальная память восстанавливает свою первоначальную форму даже после растяжения, сжатия или скручивания. Эти соединения являются идеальным решением для продуктов, которые сталкиваются с такими рисками, например, для корпусов устройств или монтажных конструкций.
Почти все эластомерные материалы изгибаются под воздействием на низких уровнях твердости, но они, как правило, становятся более хрупкими, поскольку они разработаны для повышения твердости. Полиуретановые эластомеры, которые сохраняют максимальную гибкость, являются хорошим выбором, когда технические характеристики требуют высокой твердости, в дополнение к прочности / ударопрочности. Сверхплотные термопластичные эластомеры на наружной подложке продукта могут улучшить ударопрочность, и при этом внутренняя часть изделия может дополнительно защитить чувствительные компоненты от ударов и вибрации.
Укрепляющие наполнители, добавленные к формулам смолы, улучшают механические свойства и включают:
- Стеклянные волокна
- Углерод
- Нержавеющая сталь
- Кевлар
Тонкие допуски
Различные смолы могут создавать несогласованные допуски для одной и той же части, поэтому иногда необходимо делать компромисс между ожиданиями толерантности и физическими свойствами смолы. Удерживающие жесткие допуски могут быть проблемой со многими смолами, потому что они имеют разную скорость усадки, высокие темпы теплового расширения, поглощение влаги и, в случае кристаллических материалов, могут продолжать расти кристаллы после процесса формования. Несмотря на то, что литьевые формовочные машины могут удерживать пластмассовые компоненты до жестких допусков в условиях, контролируемых климатом, эти размеры могут не соответствовать изменению температуры или влажности.
Эту характеристику следует учитывать, когда пластмассы объединяются с наполнителями, когда они должны взаимодействовать с другими типами материалов (например, с металлами), или когда конечное использование происходит в средах, где уровни температуры и влажности сильно колеблются.
Что касается поддержания жестких допусков , то в литьевой формовке рассматривают характеристики двух типов пластмасс. Аморфные пластмассы имеют случайную ориентацию полимерной цепи, что дает пластику бесформенную структуру с хорошей ударной вязкостью и вязкостью. Хорошими примерами аморфных пластмасс являются акрилонитрил-бутадиен-стирол (ABS), стирол-акрилонитрил-сополимер (SAN), поливинилхлорид (ПВХ), поликарбонат (ПК) и полистирол (PS).
Состав кристаллических пластиков представляет собой упорядоченные, плотно упакованные полимерные цепи. Это семейство пластмасс имеет более низкое удлинение и гибкость, чем аморфные пластмассы, но более высокую химическую стойкость. Хорошими примерами кристаллических пластиков являются ацетат, полиамид (ПА), полиэтилен (ПЭ), полипропилен (ПП), полиэфир (ПЭТ / ПБТ) и полифениленсульфид (ППС).
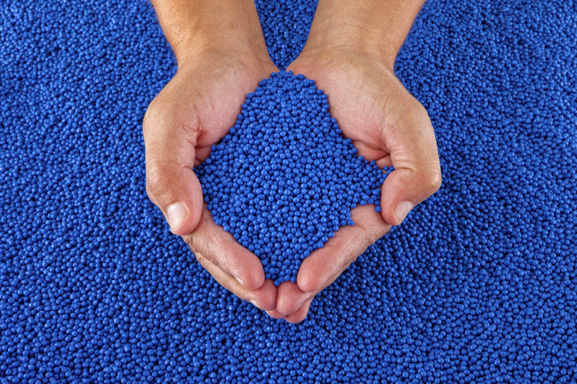
Высокая температура
Одна из самых больших проблем при использовании высокотемпературных смол заключается в том, что температура расплава чрезвычайно велика, превышая 370°С в большинстве применений. Смолы ведут себя по-разному при таких высоких температурах, что создает потенциал для деградации полимера и более низких частей, которые необходимо переделать.
Высококачественная продукция зависит от тщательного контроля температуры и выбранной смолы. Популярными высокотемпературными пластиками являются полифталамид (PPA), полифениленсульфид (PPS), полисульфон (PSU), полиэфиримид (PEI), полиэфирэфиркетон (PEEK), полиамид-имиды (PAI), этилентетрафторэтилен (ETFE) и полиэфирсульфон (PES ). Применения для этих высокотемпературных смол включают обтекатели на газоне и домашнем оборудовании, а также компоненты, расположенные рядом с блоком двигателей снегоочистителей.
Проводимость
Многие из сегодняшних проектов включают специальные литьевые формовочные смолы, которые обладают превосходной теплопроводностью, такими как коммерческие и автомобильные радиаторы, освещения LED. Эти соединения могут также использоваться в продуктах для замены алюминия. Производители этих приложений могут использовать нано технологии для производства крошечных металлических волокон и нитей, которые включены в полимерную матрицу, чтобы влиять на проводимость композиционного материала.
Поставщики материалов могут лить поликарбонатные (ПК), полипропиленовые, ABS, полиамидные 6/6 и PC / ABS смолы с проводящими волокнами из нержавеющей стали или никелированными наполнителями из углеродного волокна. Хотя литьевое формование создает сложные пластмассовые детали, которые могут быть не такими жесткими, прочными или проводящими, как заменяемые металлические детали, они подходят для применения. Кроме того, они обеспечивают другие преимущества, такие как, по существу, более легкий вес и зачастую более низкие по стоимости.
Наполнители из твердых частиц увеличивают модуль упругости и электропроводности для улучшения сопротивления теплу и ультрафиолетовому излучению. Эти наполнители также снижают затраты. Общие наполнители включают:
- Минеральные
- Кремнезем
- Керамический
- Углеродный порошок / волокно
- Стеклянные микросферы / волокна
- Порошковый металл
Уникальные характеристики
В некоторых случаях инженер-конструктор считает, что требуемые характеристики продукта четко не определены. Например, производитель, которому требуется сложный компонент утилизации мусора, должен учитывать не только производительность этого компонента самостоятельно, но и его взаимодействие с более крупной системой. В этом случае жесткий пластиковый корпус должен выдерживать жесткие требования к работе машины, а также совместим с внутренними уплотнениями и соответствующими пластмассовыми, металлическими и резиновыми компонентами.
Overmolding может помочь предотвратить утечки, но тогда выбор смолы для жесткой подложки должен учитывать материал с резиновой оболочкой. Здесь полипропилен со стеклянными волокнами может быть отличным выбором для подложки.
Сам полипропилен является относительно недорогим. Добавление стекловолокна делает деталь достаточно жесткой, чтобы выдерживать структурные требования проекта, но также совместима с материалом для формования резины. Необходима надлежащая обработка. Стекловолокно уменьшает адгезию, если его можно достичь на поверхности.
Укрепляющие наполнители улучшают механические свойства и включают:
- Стеклянные волокна
- Углерод
- Нержавеющая сталь
- Кевлар
На заводе «Инъекция Молдер»
Подобно тому, как вы являетесь экспертом по планируемой производительности ваших приложений, опытные комплексные литьевые формовочные машины имеют глубокое понимание того, как смолы производятся во время производства.
Специально подготовленные инженеры по литьевому формованию хорошо осведомлены о научном формовании, чтобы они могли лучше контролировать процессы и другие факторы, которые влияют на успешные результаты продукта. Вот некоторые сведения о критериях для литья под давлением.
Дизайн: получение процесса, связанного с процессом формования в начале процесса проектирования, имеет решающее значение для успеха проекта. Критические изменения конструкции могут потребоваться в зависимости от выбранного материала и процесса литья под давлением. В некоторых случаях выбранный материал может добавить непредвиденную выгоду для части продукта.
Например, высокотемпературные смолы очень чувствительны к номинальным стенкам и вязаным линиям. В зависимости от материала и температуры дифференциальная усадка может привести к нежелательным пустотам и другим дефектам. Опытный специалист может разрабатывать кривые вязкости для каждой конкретной смолы, чтобы имитировать процесс формования на ранней стадии, позволяя инженерам минимизировать скорость усадки и оптимизировать окончательный процесс формования.
Инструментальная сталь: для крупносерийного производства экономически выгодно инвестировать в высококачественную оснастку, чтобы избежать чрезмерного износа инструмента. Чертеж, отделка, поднутрения и типы стали должны учитываться во время разработки продукта / детали. Тип стали, выбранный для формы, будет зависеть от количества абразивных наполнителей в смоделированной смоле.
Размер пресса: машины должны быть надлежащим образом подобраны таким образом, чтобы не было превышено правильное время пребывания расплава. Слишком много времени пребывания ухудшает свойства расплава и может привести к поломке деталей с видимыми поверхностными дефектами, такими как обесцвечивание и следы ожогов.
Содержание влаги: некоторые пластмассы гигроскопичны и поглощают влагу, что может изменить поведение материала во время процесса литьевого формования. Даже небольшие концентрации влаги в расплаве могут влиять на вязкость материала, чтобы вызвать проблемы с размерами и эстетикой.
Вентиляция: правильное расположение и размер вентиляционных отверстий критически важны для последовательной обработки и для функции оснастки. Вентиляторы позволяют задерживать воздух и летучие вещества от выхода из инструментальной полости. Повышенная концентрация летучих веществ может быстрее расширять вентиляционные отверстия и вызывать пластическую хрупкость, ожоги, другие дефекты поверхности и плохую прочность линии вязания, что снижает качество и производительность детали.
Охлаждение: Охлаждение – это, пожалуй, самый важный этап процесса формовки, особенно для применений с использованием высокотемпературных смол. Выбор правильных техно-конвейеров, горячего масла и воды под давлением предотвращает негативные воздействия, начиная от переменной усадки и заканчивая нечеткой стабильностью размеров. Например, нейлон чрезвычайно восприимчив к деформации, но опытный инженер по литьевому формованию будет знать, где разместить охлаждающие каналы в инструменте для контроля и предотвращения этого.
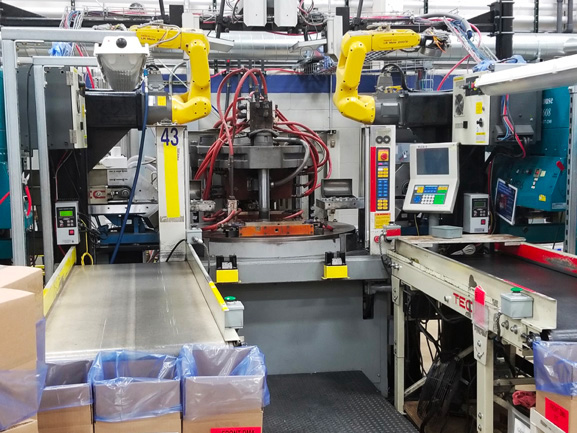
Пластмассы расширяют возможности вашего дизайна
Требования рынка приводят к разработке продуктов, которые являются прочными, обеспечивают высокую производительность и предлагают улучшенную эстетику. Массив соединений смол означает, что дизайнеры могут расширять свои фантазии, чтобы обеспечить оптимальное удобство использования продукта, совместимость, внешний вид и выносливость.
В случае обилия выбора пластмасс, выбор материала является меньшей помехой и большей возможностью превзойти ожидания продукта. Поэтому в интересах проекта вначале разработать рекомендации для партнера по литьевому формованию для определения материалов, которые могут соответствовать стандартам продукта или части, которые имеют в виду разработку продукта. Эти обсуждения касаются не только того, что материал может или не может сделать, но и того, как дизайн может реагировать на возможности пластических соединений, которые вы имеете в виду.
Работая в тесном контакте с инженерами-конструкторами, опытный комплексный литьевой формовщик может понять требования к продуктам и проанализировать пригодность выбранных материалов. Этот активный подход приводит к более успешному и экономичному проекту.
Автор
Аль Тимм – старший инженер по развитию бизнеса корпорации Kaysun, предлагающий заказчикам индивидуальные литьевые и инженерные решения для проектирования, производства и сборки сложных, прочных пластмассовых деталей.
No Comments
Sorry, the comment form is closed at this time.